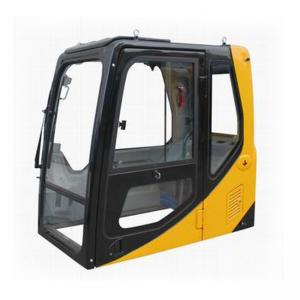
Add to Cart
Engineering mechanical or the parts for the black electrophoretic paint
Product Introduction
1.HLS-1701BLB/HLS-1701B Black Cationic Epoxy Electrocoat for auto is a new generation electrophoretic coating researched and developed by HLS Paint (Shanghai) Co., Ltd.
2.It represents modern technology of cathodic electrophoretic coating that is environment-friendly with high property and low cost. Such coating does not contain heavy metal like lead, tin, cadmium and mercury etc. It is a two-component, water-dispersed resin,meanwhile, it took in features of previous products, and can adapt galvanized steel sheet perfectly, almost can be applied to foundation coating of all metal, such as: cold and hot rolled steel sheet, galvanized steel sheet, aluminum products and stainless steel sheet etc.
This product features shown below:
Good stability of bath can adaptable for a longer updating cycle. | Coating fullness of good, better substrate hiding . | Strong anti-corrosion properties, good salt spray resistance workpiece edge. |
Main ingredients
Additives: surface active agent, prevent shrinkage cavity agent | |
Solvent: alcohol ether | Neutralizing agent: organic acid |
Filling tank proportion and method
Coating conditions
Experimental panel: phosphated cold-rolled steel plate
Tank temperature: 30-36℃
Pole ratio: A/C = 1/2 ~ 1/4
Distance of electrodes: 15cm
ED time: For full immersing 1-3 minutes ( 20 seconds soft start)
Baking conditions:(180-190)℃×(20-30)min (Keeping temperature of parts coated)
Product film performance
Project | Indicator | Test standard | |
Appearance | Normal / abnormal | Normal | Ocular estimate |
Hardness | ≥ | 2H | GB/T 6739 |
Cup drawing | mm ,≥ | 6 | GB/T 9753 |
Adhesion | Level | 0 | GB/T 9286 |
Flexibility | mm | 1 | GB/T 1731 |
Impact | kg·cm | 50 | GB/T 1732 |
Gloss | 60 | 50-80 | GB/T 9754 |
Water resistance | h,(23±2)℃,≥ | 240 | GB/T 1733 |
Acid resistance | h,(50g/L H2SO4),≥ | 72 | GB/T 9274 |
Alkali resistance | h,(50g/L NaOH),≥ | 48 | GB/T 9274 |
*Salt spray resistance | h,(film thickness ≥ 20μm) ,≥ | 1000 | GB/T 1771 |
* Note: The substrate use the Bonder standard phosphating steel panel, crossed out unidirectional expansion eclipse ≤ 2mm.
Customers in the engineering machinery